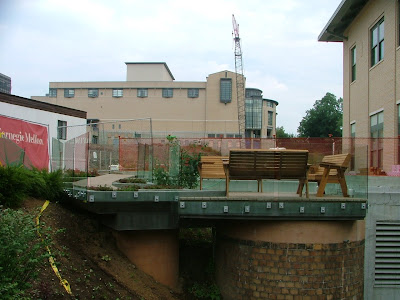
This is the most complicated project I have been involved with and certainly the coolest. This cantilevered concrete slab seating area was constructed as part of my Design and Construction course during my senior year at Carnegie Mellon. The project was a memorial to
Allen Newell, a CMU computer science professor and AI pioneer. This project was designed and built by CMU students, though the majority of the credit goes to Professor Larry Cartwright of the Dept. of Civil and Environmental Engineering. He was by far the best teacher I've ever had. As the ancient proverb says:
"Concrete doesn't fail at 3000psi, it fails when Larry Cartwright tells it to"
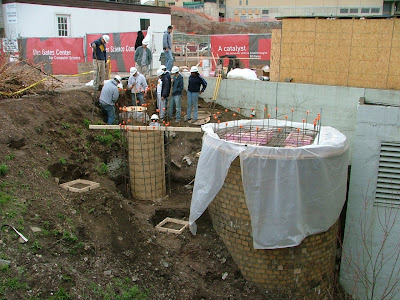
The site was on a steep slope in front of the current Computer Science building on campus, and obviously provided many challenges. The building formerly was the US Bureau of Mines facility and had two 90-100ft smokestacks in front of it. When the school acquired the building, the smokestacks were truncated and capped to the elevation you see above. This truncated structure was our site and would become the foundation for the entire project. Three piers were poured leading up to street grade to support the alternating square slab design that was chosen.
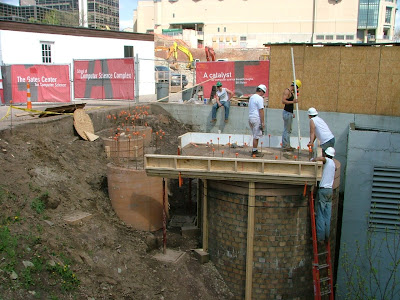
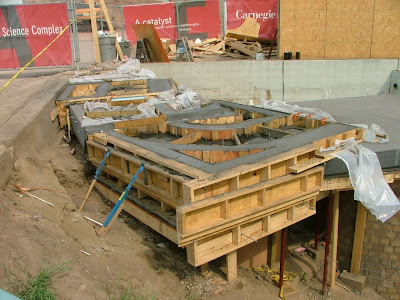
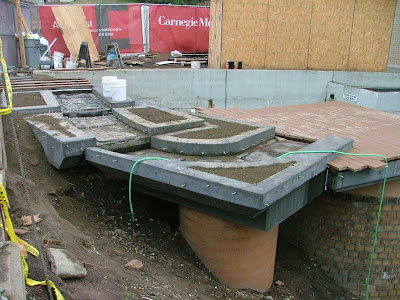
We designed our own form-work and poured the concrete ourselves. The concrete slabs have planters sunk into them and a handicap accessible ramp runs through the four alternating squares.
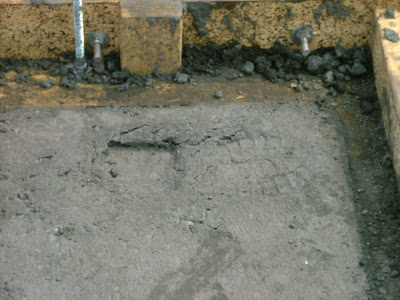
I left my permanent footprint below where the ramp would be strung.
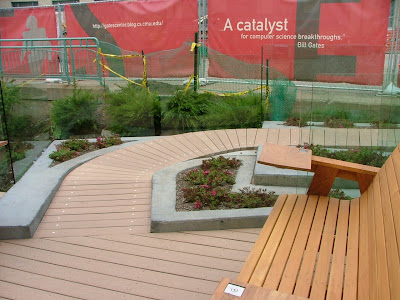
I spent an extra month at school during the summer to see the project to completion. We used Trex, a material consisting of recycled wood and plastic, to deck the ramp and sitting area. I had custom cut each board on the ramp to fit the curve in a process that took nearly a week but ended up looking fantastic. We put sedum, a durable breed, in the planters.
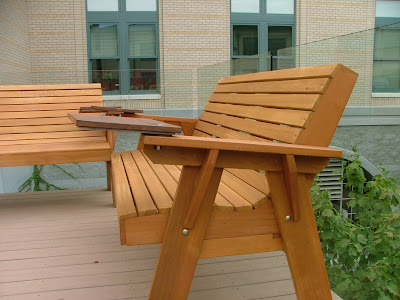
We custom made these benches out of cedar with mahogany swing tables for laptop use. We designed the slope of the benches specifically for comfort and the finished product was beautiful. In the end, these are likely the three most expensive and well thought out benches in Pennsylvania.
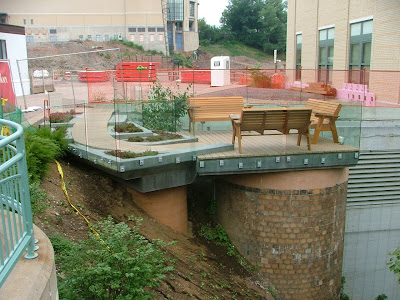
The project was finished with custom made finished glass (the only thing we didn't fabricate and install ourselves). The glass was etched with the names of everyone in the class and prominently with a quote for Allen Newell:
"To each scientific life its own style: and each style defines a life"
We also landscaped the site around the platform with ivy and native plants. Along the wall behind the structure we installed a stainless steel "living wall" system to encourage ivy growth to hide the concrete walls. The site has both electrical outlets and wireless internet access. It is a fantastic testament to a bunch of very talented students and an extraordinary professor.
Check out the webpage:
Allen Newell Garden